Project Results
The project "The integration of the new data and technologies from the domain of performing materials and new generation production of centrifugal rotors included in turbo machines" aim is to developed a new material for the completion of the centrifugal rotor from turbo machines composition.
The material that is running centrifugal rotors must meet a number of characteristics: high mechanical resistance ( s r ), the limit of high flow ( t 02 ) near the mechanical resistance (the rotor must not be deformed as it reduces production and gap seizure which led to the destruction of entire turbo machine ), the elongation (A%) and resilience (KCU) high. Material must also possess features good corrosion and wear. At this time, the international market of the rotor is used (for strong parts required - such as those covered by the project) with a material called 17-4 PH, a precipitation steel with copper. This alloy is very difficult to achieve, is not used in Romania than the COMOTI and the extremely rare MApN, all the producers (which lately has been reduced to COS Targoviste) will not develop this alloy because infests the oven lining with copper and cannot produce other alloys.
From technologically point of view this alloy is very difficult to use, is likely micro cracks, heat treatment is difficult, etc..
In these conditions COMOTI was forced to think a viable alternative because of the import purchase price of the rotor will eliminate him from the rotary machines market.
Together with UPB, UPG, METAV-CD COMOTI was examined multiple ways to reach a type of alloy that can be promoted successfully on the market of materials for rotors.
It is a medium alloy steel, having in composition Cr, Mo, Mn, Ni, Si, V, no standards in Romania and the EU in its mechanical properties are fully comparable to the 17-4 PH alloy, other tests up to this date, on the corrosion and wear resistance is much closer to those of 17-4PH.
This material was promoted by COMOTI in an important international project “METHOD”, in which they were designed and executed in this material four centrifugal rotors which, after having been tried and tested in Romania, were sent to another important partner of contract-NUOVO PIGNONE Italy where they were tested and stands the test, the results were very good which he encouraged.
The high speed centrifugal rotors have been achieved by a new concept of calculation and design solutions related with original control and processing solutions in order to improve their performance and characteristics.
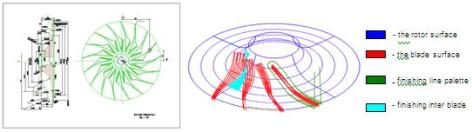
The r otors, a complete set of five centrifuge rotors, were made by precision casting process, applying a special technology with its own aim reach the level of quality, particularly high, required by these pieces.
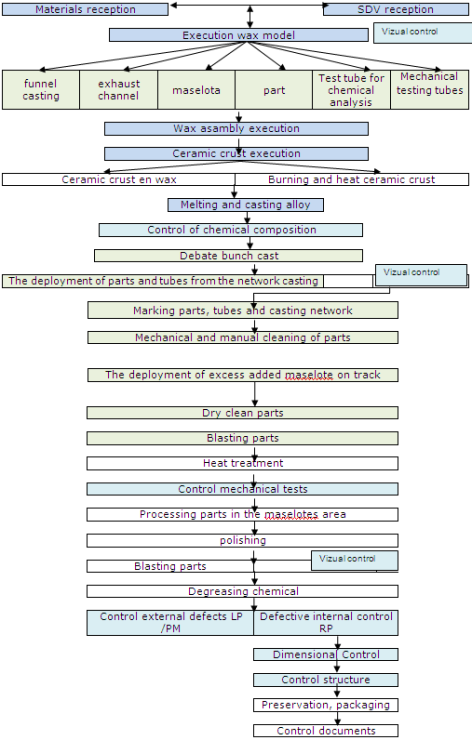
The gas-dynamic surfaces of the rotor (aero-foils and the palettes that come into contact logs) have undergone a process of coating the surface type HVOF with materials to improve resistance to wear and corrosion.
|